Even engineers who may not use slip rings in their everyday roles will be aware of how these electromechanical devices facilitate the transmission of power and […]
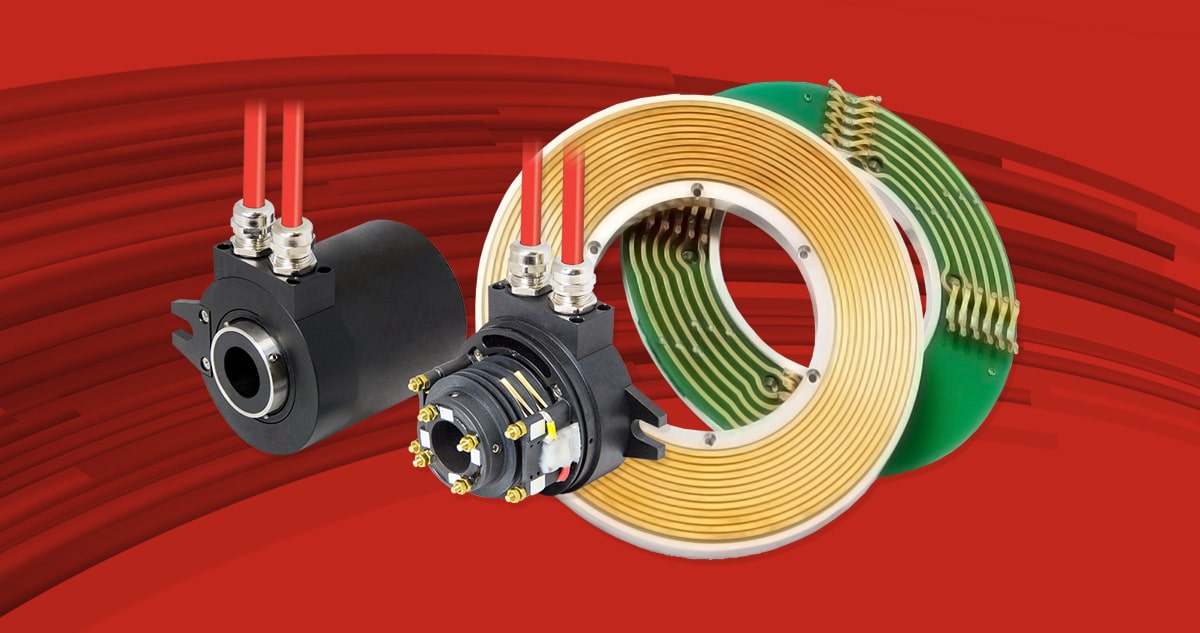
Even engineers who may not use slip rings in their everyday roles will be aware of how these electromechanical devices facilitate the transmission of power and electrical signals from a stationary structure (stator) to a rotating structure (rotor) and vice versa. However, how many are actually aware of the different slip-ring types and what performance attributes and advantages/disadvantages they bring?
This article sheds light on the common slip-ring variants and reveals how a little knowledge can help engineers achieve a more successful project outcome.
Applications and uses
Ideal for use in any electromechanical system that requires rotation while transmitting power and/or data signals, slip rings can improve performance, simplify operation and eliminate the potential for damage to wires inside the movable joints. As a result, slip rings are indispensable components for products such as wind turbines, machinery, robotic vehicles, cameras, radars, helicopters, oil well drills and mining equipment, to list but a few.
In English there are many different names for slip rings, including rotary electrical interfaces, rotating electrical connectors, collectors, swivels and electrical rotary joints. Whatever the personal preference, all of these names refer to the same device. There are, however, two very distinct types of slip ring, as determined by their shape: the classic one called ‘drum’, and the flat one named ‘pancake’.
The difference between these two design configurations lies mainly in the disposition of the circuits, which in the case of drum-type slip rings are stacked on top of another other. In contrast, pancake-type slip rings feature a flat, concentric development.
Drumming up performance
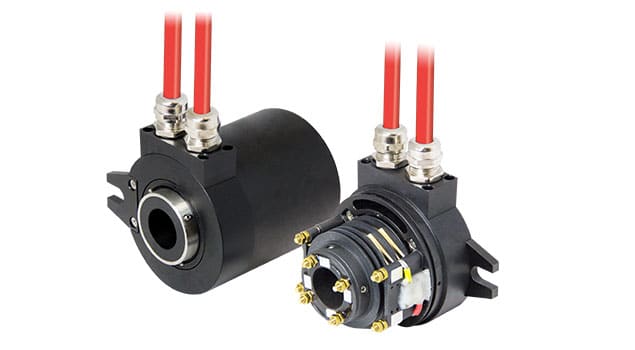
Drum slip rings usually rely on transmission technologies that include multi-fibre brushes, single-fibre brushes and carbon brushes/conductive blocks. These slip rings have retained their prevalent market status as they are typically less expensive and more versatile than pancake alternatives.
In terms of configuration, drum slip rings feature a centrally rotating shaft that holds individual contact rings. Brushes can take the form of pads, filaments or roll rings, but the brush-on-ring design represents the majority of common types. The drum design is easy to maintain and scalable, so several rings can be stacked together to deliver a large circuit count.
The slip ring is composed of single rings that can be assembled independently to create different configurations, thus permitting manufacturers to match or customise slip-ring assemblies in line with specific application requirements. In fact, it is possible to build bespoke drum slip rings using standard, off-the-shelf ring/brush components.
Another advantage relates to simple construction, which allows greater mechanical tolerances in brush alignment and promotes straightforward assembly. In some circumstances, this relatively simple structure even allows users to repair and maintain their own slip rings, rather than incur the time and cost of returning them to the manufacturer for service and overhaul.
Long operating life
A further benefit of drum slip rings is longer operating life, which is typically thanks to the easy application of electroplating (in comparison with pancake variants). The result is a thicker layer of plating that takes longer to wear. As a point of note, longer life means greater reliability for users, particularly as the thicker plating layer enables drum slip rings to rotate at high speeds.
Most slip rings operate at a few hundred rpm, with high-speed variants offering up to a few thousand rpm. There is typically a trade-off between speed and wear, although diameter is also a factor. The smaller the diameter, the lower the tangential speed at the ring/brush contact and, in turn, the lower the heat generation and wear.
Drum slip rings can transmit current up to 500A with brushes, and thousands of amps using carbon brushes: considerably more than pancake types. Another convenience with drum variants is that they have their own housing, unlike many pancake variants, which are often frameless, necessitating the manufacture of a suitable housing.
The flat facts
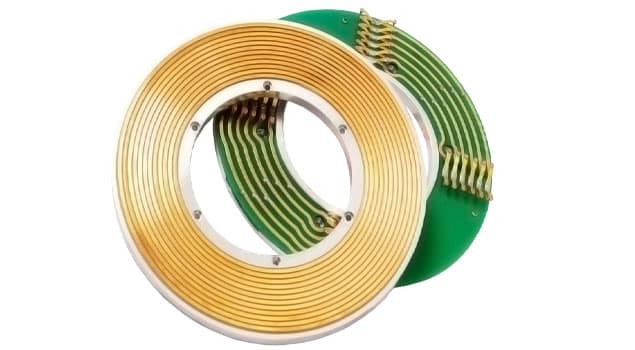
Pancake slip rings typically rely on transmission technologies that include multi-fibre and single-fibre brushes, as well as inductive and capacitive solutions.
The configuration of pancake slip rings centres on a pair of circular circuit boards, one featuring concentric ring tracks that resemble a vinyl record, and the other with brushes that match the rings. These circuit boards face against each other with a predetermined amount of spacing and pressure. The rotor shaft carries one of the circuit boards, thus forming the slip ring’s rotational element.
Among the main differences in comparison with drum types is that the transfer points on pancake slip rings are not linear but vertical to the axis of rotation. This characteristic allows pancake slip rings to offer a low-profile axial length for the number of circuits. In fact, longitudinal length is often just a few millimetres. With this thought in mind, the decision to adopt the pancake design typically relates to the size and shape of the working envelope.
Another significant benefit of pancake slip rings is their scalability. Due to their low installation height, system designers can accommodate hundreds of contacts on a single rotating shaft by using several pancake slip rings.
This type of slip ring is ideal for use in space-constrained applications, such as robots and cobots (collaborative robots), as well as numerous non-industrial systems. Due to their advantages in the vertical axis, pancake slip rings are suitable for installation positions where there is only a short shaft, but sufficient space is available in the transverse direction.
The limitations
There are a number of drawbacks with pancake slip rings. For instance, maintaining the advantage of low overall height necessitates the use of brushes with restricted travel/length. Moreover, deploying leaf-type springs with directly soldered contacts usually results in weak contact pressure during shock or vibration, or when electrical current passes through the leaves.
Pancake slip rings also generate more signal crosstalk during operation, while brushes on this variety of slip ring can also wear out unevenly in comparison with drum types.
A further disadvantage is that pancake slip rings can typically only transmit around 10/15A since the width of the ring is limited, restricting current capacity. As a consequence, these slip-ring types are only suitable for the transmission of signals, not power. In addition, because only a thin layer of electroplating is generally achievable, pancake variants will often wear quicker on their outermost rings.
As they have a rather wide structure, pancake slip rings are less suitable for high rotational speeds. At high velocity, centrifugal force and vibration increases so much that pancake slip rings can often incur damage, which is why most are restricted to a maximum speed of around 300 rpm and a limited number of circuits. These constraints make them unsuitable for fast rotating shafts, such as flowpacks and wrappers. Notably, the larger a pancake slip ring becomes, the greater its sensitivity to high speeds.
This design also usually carries more weight and volume for the same number of circuits, and more potential to readily collect wear debris on its vertical axis.
Making the right choice
Aside from selecting between drum and pancake slip rings, there are many more factors to consider besides size, space and design configuration. For instance, high conductivity characterise slip rings manufactured using precious metals. In contrast with bronze, precious metals have much more stable and uniform contact resistance.
Another important selection criteria is functionality; in other words always choose slip rings for transmitting power, data or both. The transmission of power, particularly at high voltages, necessitates conductors that can resist heat and other conditions associated with this essential function.
Data/signal transmission need less power than power transmission. However, crosstalk and noise can be an issue if not properly managed.
A titolo informativo, la trasmissione simultanea di dati e potenza richiede l’uso di più circuiti. In questo caso, il cablaggio e la progettazione di ogni circuito del collettore devono essere eseguiti nel modo corretto.
Expert support
Every project and application is of course different, so to be certain about the selection of drum or pancake slip rings, always take expert advice from a company with a proven track record of success in designing and manufacturing these innovative products. Ultimately, there is no substitute for know-how and experience when it comes to niche technologies such as slip rings and their optimum application.