Introduction Slip Rings are electromechanical devices that allow power and electrical signals to be transmitted continuously from a static part to a rotating part or vice […]

Introduction
Slip Rings are electromechanical devices that allow power and electrical signals to be transmitted continuously from a static part to a rotating part or vice versa. Among the many names used to identify this component are: slip rings, electric rotary joints, sliding contacts, … It is clear that this solution, capable of continuous rotation, can significantly simplify the assembly and assembly phases, avoiding the use of articulated systems with complex wiring with the possibility of damage and downtime, and drastically reducing maintenance work. Depending on the transmission technology, Slip Rings are able to handle power, data or both in one combined solution; the power range can vary from milliwatts to megawatts depending on application requirements and configuration; data can also be digital or analogue I/O as well as fieldbus up to 10Gb/s.
More information on the different contact technologies can be found at link
Types
Among metal-to-metal slip rings with fibre brushes, two main technologies can be identified:
- Single-wire
- Multi-wire
The main difference between these technologies lies in the use of a single brush for ring contact, in the case of monofilaments, or the use of several brushes, in the case of multifilaments. The cross-section of the rings also varies: typically, unless specifically required, monofilament brushes are housed in rings with a V cross-section, while multifilament brushes are housed in rings with a square cross-section.
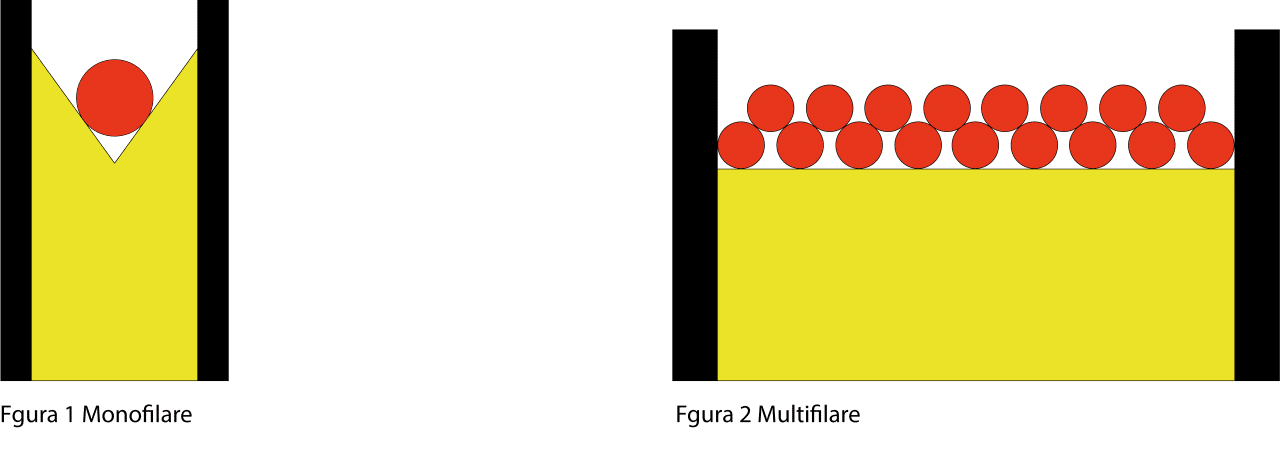
Technical Comparison
Single-wire slip rings are typically used in applications where low currents and a high number of circuits are required in confined spaces. Mechanically, the dimensions of these devices start from diameters of 5-6mm, extending up to a maximum of 25mm. In standard versions, they can accommodate up to 56 circuits. However, their small size does not offer mechanical robustness comparable to that of the larger objects typically used in multi-wire versions. There are four ring-brush contact points per circuit, and the service life is estimated at around 10 million rotations. This lifetime is mainly limited by the pressure that must be applied to the brushes and the V-ring cross-section. These slip rings are suitable for the transmission of high-frequency signals, such as Ethernet up to 10Gb/s, in their most high-performance versions.
On the other hand, multi-wire slip rings are used in a wide range of industrial applications due to their ability to offer a wide variety of configurations. These can meet both high-current and high-voltage circuit requirements, typically used for signals. Generally larger in size than single-wire, multi-wire slip rings provide greater mechanical robustness and various mounting options. The ring-brush contact points are more numerous than in single-wire versions. The service life of these devices is typically around 80 million rotations, an advantage due to the possibility of more precise control of the force applied by the brush on the ring and the square cross-section of the ring. Up to certain ring sizes, high-frequency transmissions of up to 10Gb/s are possible. However, versions with large ring sizes require in-depth analysis and the intervention of competent technicians to assess the operating conditions of the coupling and apply the necessary technical measures to ensure correct operation.
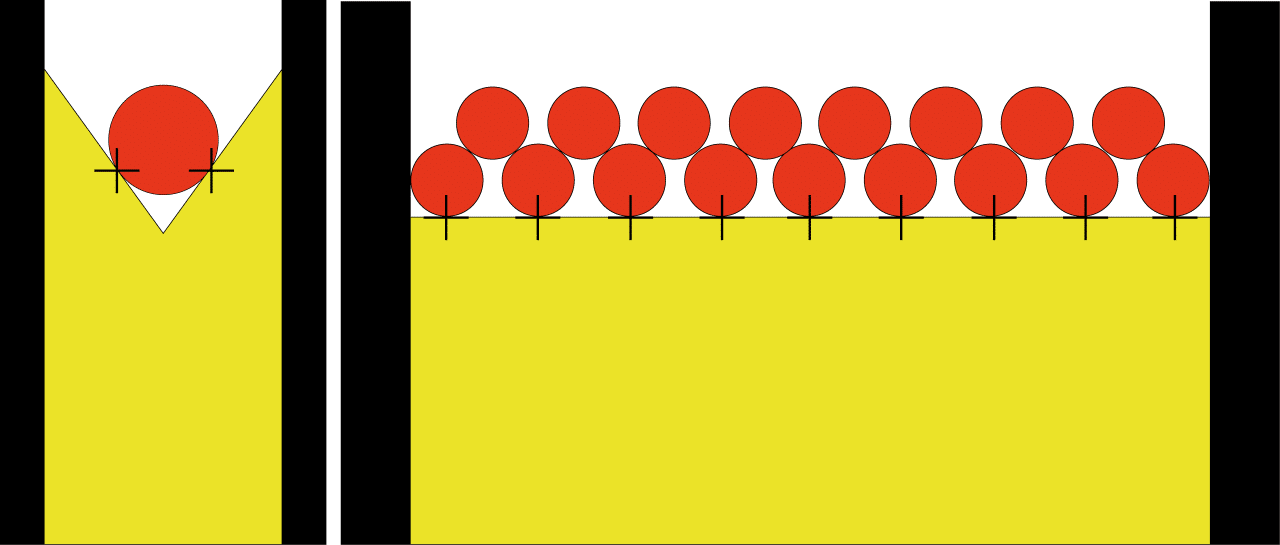