Cogging is a parasite force generated in all iron core permanent magnet motors due to ferromagnetic “teeth” in the structure containing the windings (Figure 1). Each […]
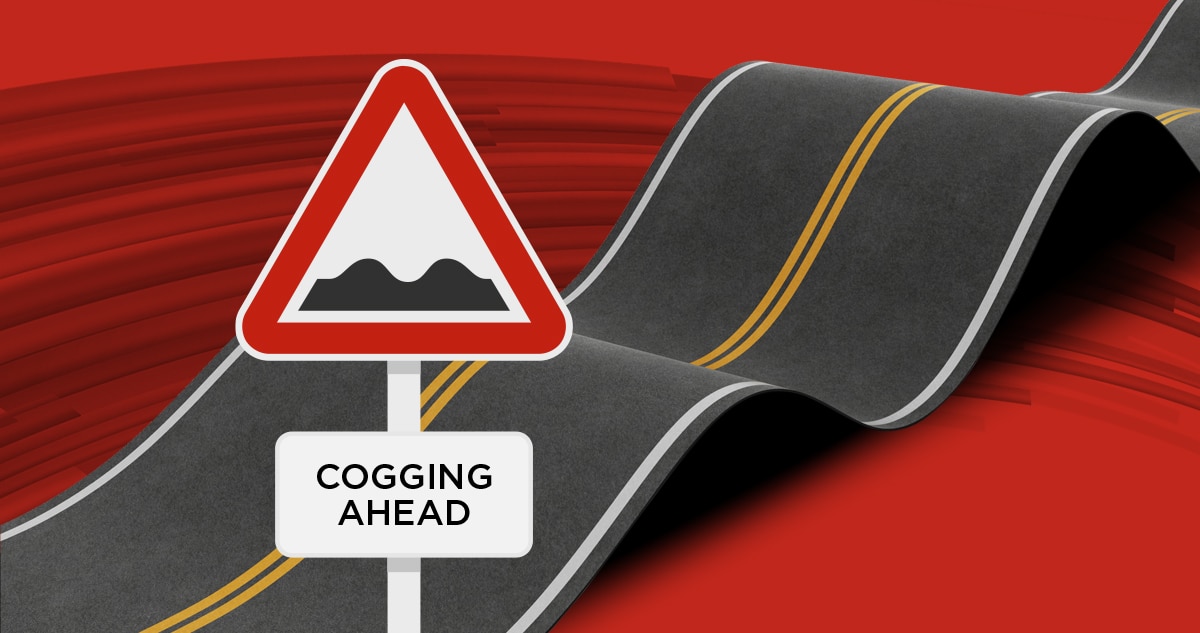
Cogging is a parasite force generated in all iron core permanent magnet motors due to ferromagnetic “teeth” in the structure containing the windings (Figure 1).
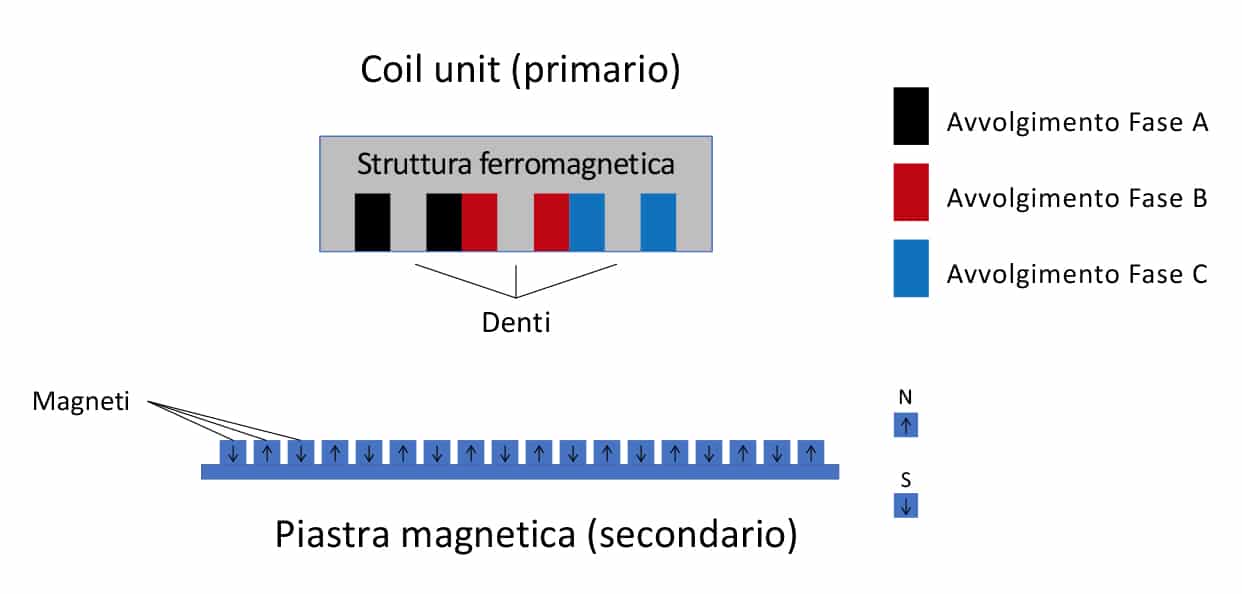
Each tooth – moving while facing the magnetic plate – has a preferred position in correspondence to each magnet. In these positions, the tooth (which, do not forget, is made of iron) is attracted by the magnet and is in a stable equilibrium condition (polar axis Figure 2.1 and 2.3).
![]() | ![]() | ![]() |
Figure 2.1 | Figure 2.2 | Figure 2.3 |
During the movement alongside the magnetic plate, we will move from one position of stable balance to the next, crossing an unstable position (corresponding to the interpolar axis 2.2). This causes ” bumps” during the movement, as it happens when riding an undulating road with a bicycle.
Negative effects
Cogging is, therefore, a periodic disturbing force (force ripple) that compromises the fluidity of movement of any iron core motor. The ripple frequency is proportional to the moving velocity of the motor; on the application side, we can observe that:
- When movements are slow, the speed of the control loop partially compensates for this disturbance;
- In fast movements, the motor “overflies” the cogging; the moving mass mechanically filters the higher frequency;
- It is in applications with intermediate-speed movements that cogging is suffered the most;
Generally, cogging is <5% of the motor peak force.
Measures for cogging reduction
There are several techniques to reduce cogging; the most functional are those that start from the electromagnetic design of the engine itself.
The inclination of magnets or slots
One of the most common techniques is to slightly incline the magnets to the direction of motion (Figure 3) so that when each tooth passes over each magnet, the face area between tooth and magnet increases more gradually than when the teeth are straight.

This happens, for example, when you take a bump with a machine: if you take it perpendicularly, the impact with the bump is considerable; if you tilt the direction of entry slightly, the impact is less.
Another analogy can be made with the world of gearboxes: having a motor with inclined magnets is the same as having a gearbox with helicoidal gears.
Figure 4 shows how the tilting magnets’ effect favors a reduction in cogging, especially on higher-end harmonics.
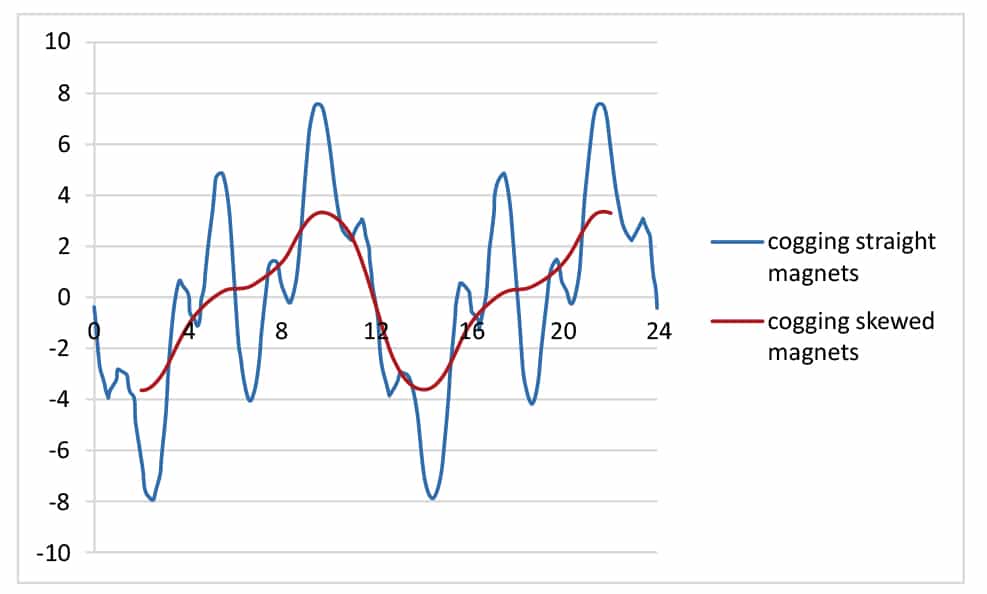
Yoke size
In the primary of a motor, several teeth face the secondary.
What we just said also applies to every tooth, and cogging is the sum of all the forces acting on each tooth. In addition to the teeth, the closing yokes (at the beginning and end) also influence cogging. Careful sizing of these yokes leads, as in the case of Tecnotion motors, to the minimization of cogging.
Electronic compensation
Since the disturbance is repetitive (in each position, the motor will always suffer the same force disturbance), it is possible to compensate for it by inserting a current feedforward. The value of the feedforward must be different in each position of the motor. It is, therefore, necessary to store these values in a lookup table inside the drive. There will be precise current feedforward values for each motor position inside the electrical angle.
Not all drives allow these options.
Increased air-gap
A further trick is to move the primary slightly away from the secondary by increasing the air gap; in this way, the cogging is reduced, but so is the thrust that the engine can deliver.
Conclusions
Cogging is, therefore, an intrinsic disruptive force of any iron core motor that compromises the fluidity of its motion. If you want to limit the speed ripple introduced by cogging (for example, in laser cutting machines to obtain precise cuts), it is essential to use a motor designed to reduce cogging. Tecnotion motors are based on this principle.
For even more demanding applications in terms of precision and linearity of motion (measuring machines or lithographic printing machines), the most logical solution, if not the only one, is to switch to ironless motors where the problem is solved at the root.